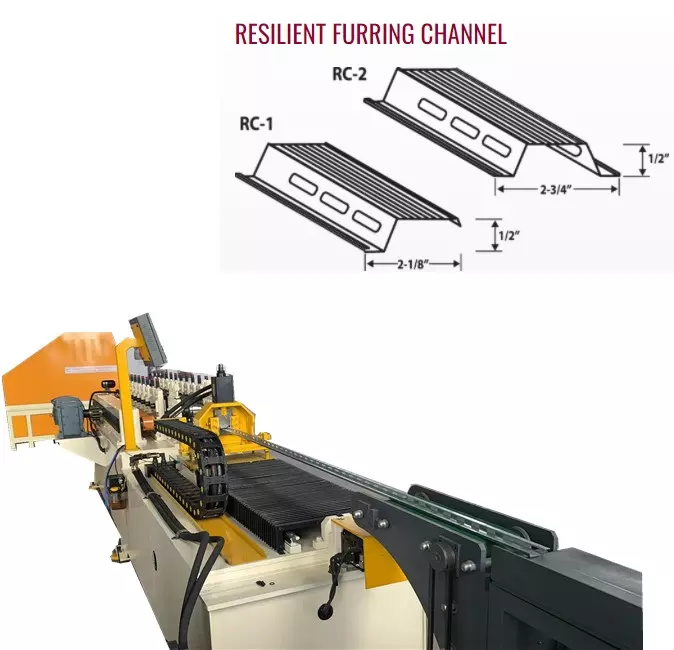
Product Profiles Details
– Dimensions: 2-½ inches wide and 12 feet long.
– Depth: ½ inch.
– Thickness: 18 mils.
– Design thickness: 0.0188 inches.
– Capable of reaching speeds up to 70 m/min, even during punching operations.
– Equipped with a dual-head decoiler for easy coil changes and high-speed processing.
– Utilizes rotary punching instead of standard CNC punching, resulting in lower noise and higher speed.
– Constructed with 16 roller stations and includes a servo tracking system.
– Features an integrated packaging unit for quick and efficient packaging.
– Fully automated production line, allowing efficient operation with a single worker.
– Controlled by a PLC system, designed for ease of operation and high productivity.
Features of the (1/2″ HEIGHT) Furring Channel Roll Forming Machine:
The resilient channel should be mounted perpendicular to the framing members, with the RC-1 or RC-2 attachment flange positioned along the bottom edge. These channels come pre-punched to facilitate screw attachment to either wood or steel framing, while nails are not recommended for securing the RC-1 Pro resilient channel to framing members.
Designed as a slim metal channel, resilient channel significantly enhances the sound insulation of drywall, sheetrock, plasterboard walls, and ceilings. By isolating drywall from the framing studs, it effectively reduces sound transmission.
The RC-1 and RC-2 channels are among the most affordable and efficient solutions for improving sound transmission loss in both wood and steel-framed walls and ceilings. These channels are used as cross-furring components to resiliently attach gypsum, with a knurled surface that simplifies the attachment of wallboard with screws.
The RC-2 double-leg resilient channel is particularly suited for ceiling installations involving multiple layers of gypsum board. As with other resilient channels, it should be installed perpendicular to the framing members and features pre-punched holes for secure screw attachment to wood or steel framing members.
Here are the key features and components of Resilient Channel Roll Forming Machine:
Entry and Feeding System: The machine typically includes a mechanism that allows the metal strip to be loaded and fed smoothly into the roll forming section.
Roll Forming Stations: These stations form the core of the machine and consist of multiple rollers and dies arranged in sequence. Each station gradually shapes the metal strip, with each one performing a specific operation. For hat channels, the stations bend the strip progressively to achieve the required profile.
Cutting Mechanism: Once the metal has been shaped into a hat channel, a cutting mechanism is often integrated to cut the formed channel to the desired length.
Control System: Most modern roll forming machines are equipped with computerized control systems that let operators set parameters such as the hat channel’s dimensions, the speed of production, and other settings.
Material Handling and Output: After production, the completed hat channels are typically transported out of the machine via a conveyor or material handling system for further processing or packaging.
Hat Channel Roll Forming Machines are widely used in industries such as construction, automotive, and manufacturing, where hat channels are used as framing or structural components. These machines offer consistent dimensions and high production efficiency, making them essential to many production processes. The machine’s design and specific capabilities vary based on the manufacturer and application needs.
Hat Channel Profile: A hat channel profile, also referred to simply as a “hat channel,” is a metal framing or support component used in construction and various industrial applications. Its name comes from its distinctive shape, which resembles a “U” or a hat when viewed in cross-section.
Profile drawing:
CEMCO’s standard RC1 resilient channels are manufactured with a 1-1/4” top flange, and a 1/2” nailing/screw attachment flange, giving the channel 1/2” furring height from the face of the wall stud.
The Technical Specifications Of The Resilient Channel Forming Machine:
ZTRFM Resilient Channel Machine |
||
1.Formed Material | PPGI,GI | Thickness:0.4-0.8mm |
2.Decoiler | Hydraulic automatic decoiler | Manual decoiler(will give you as free) |
3.Main body | Roller station | 12 rows(As your requirement) |
Diameter of shaft | 50 mm solid shaft | |
Material of rollers | 45# steel, hard chrome plated on the surface | |
Machine body frame | Metal steel welded | |
Drive | Gearbox transmission | |
Dimension(L*W*H) | 7800*800*1200(customize) | |
Weight | About 4.5T | |
4.Cutter | Automatic | cr12mov material, no scratches, no deformation |
5.Power | Motor Power | 7.5KW*2 sets |
Hydraulic system power | 7.5KW | |
6.Voltage | 380V 50Hz 3Phase | As your requirement |
7.Control system | Electric Box | Customized(famous brand) |
Language | English(Support multiple languages) | |
PLC | Automatic production of the whole machine. Can set batch, length, quantity, etc. | |
18.Forming Speed | Max 70m/min(include punching holes,customized) | Different speed designs for options. |
More pictures of the machine:
Light Gauge Steel Framing Machine Specification Width(web): 89mm Height(flange): 41mm Lip:7-12mm The machine match with 3 sets punching die(75~96/138-159/180-200)mm […]
The primary advantages of using steel roof and ceiling battens include: Raw material: GI Hardness […]
Angle bead is commonly used where walls meet walls or ceilings, over inner angles of […]
Stud And Track Roll Forming Machine 1) Profile width: 3″/3.5″/3.625″/4″/5.5″/6″ 2) Profile flange: 1 1/4 […]
STAY IN THE LOOP