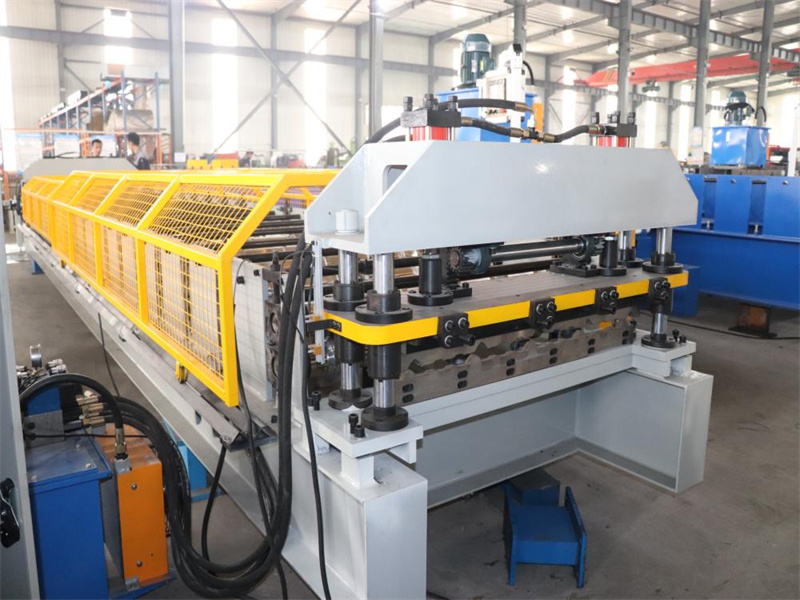
Technical Parameters of R-Panel:
15 Stand Roll Former
4 Rib 36″ x 1 1/4″ High Ribs
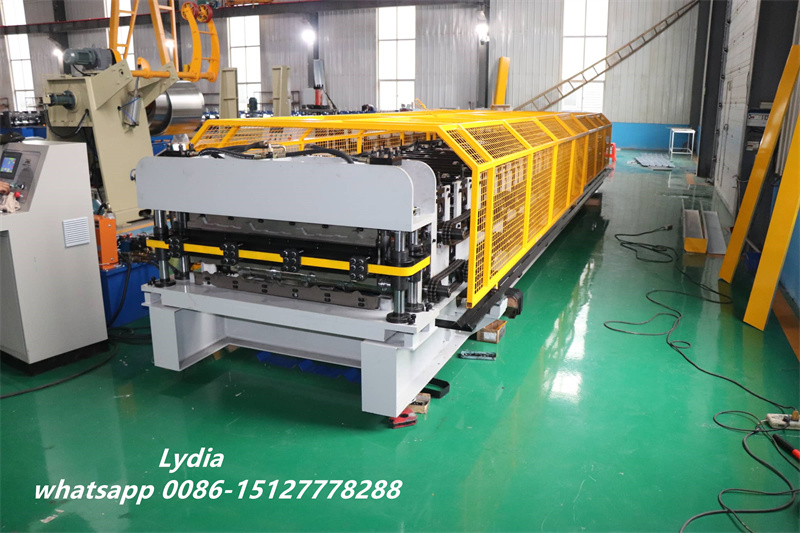
PBR Panel R-Panel Machine
Drawing profiles:
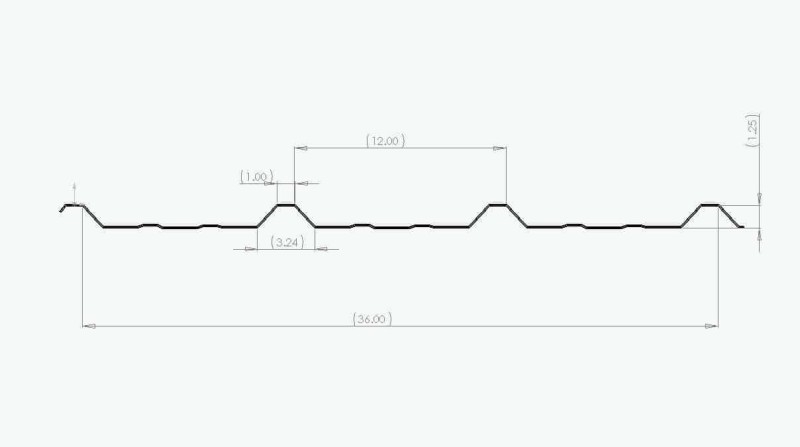
PBR Panel Roll Forming Machine
R-Panel Roll Forming Machine Overview
An R-Panel Roll Forming Machine is a specialized piece of equipment designed to produce R-Panel, a type of metal roofing and wall panel that is widely used in the construction of pre-engineered metal buildings. These panels are known for their durability, high wind resistance, and low maintenance requirements, making them an excellent choice for industrial, commercial, and agricultural applications.
Specifications for 36″ AG Panels:
– Width: 36 inches (914 mm) wide, which is a common size for agricultural and industrial buildings.
– Material: Typically made from galvanized or prepainted steel, depending on the application and desired finish.
– Profile Depth: Varies based on the specific profile, but generally ranges from 1.5 to 2.5 inches (38 to 64 mm).
– Rib Height: The height of the raised ribs can vary, but it typically ranges from 0.5 to 1 inch (13 to 25 mm), contributing to the panel’s rigidity and aesthetic appeal.
– Length: Panels can be produced in various lengths, often customized to fit the specific building dimensions.
How the R-Panel Roll Forming Machine Works:
- Uncoiling System: The machine starts by uncoiling the metal sheet (usually steel) that will form the base material for the R-Panel. This system ensures a smooth and continuous feed of material into the forming process.
- Pre-punching (Optional): If required, the machine can include a pre-punching station to create holes or other features in the panel before forming. This is useful for fastening or ventilation purposes.
- Roll Forming Stages: The metal sheet passes through a series of roll forming stations, each progressively shaping the material into the final R-Panel profile. The rolls are precision-engineered to create the characteristic ribs and flat sections of the R-Panel.
- Cut-off Mechanism: Once the panel has been fully formed, a cut-off mechanism severs the panel to the desired length. This can be done automatically based on programmed settings or manually as needed.
- Stacking or Packaging: After cutting, the panels can be stacked or packaged for transport or immediate installation. Some machines include automated stacking systems to streamline this process.
- Quality Control: Throughout the production process, the machine may incorporate quality control measures such as thickness gauges, alignment sensors, and surface inspection systems to ensure consistent product quality.
Full-Automatic T18/T35 IBR Roofing Sheet Roll Forming System with Dual-Layer Capability This advanced roll forming
LED Light Box Profile Roll Forming Machine The Component Specifications of this roll forming system
1100 Series High-Speed Automated Roll Forming Line Integrated Production Line Configuration Manual Decoiler → Roll Forming Unit → PLC
This machine manufactures roofing panels featuring single snap-lock seams, designed for rapid assembly without the
STAY IN THE LOOP