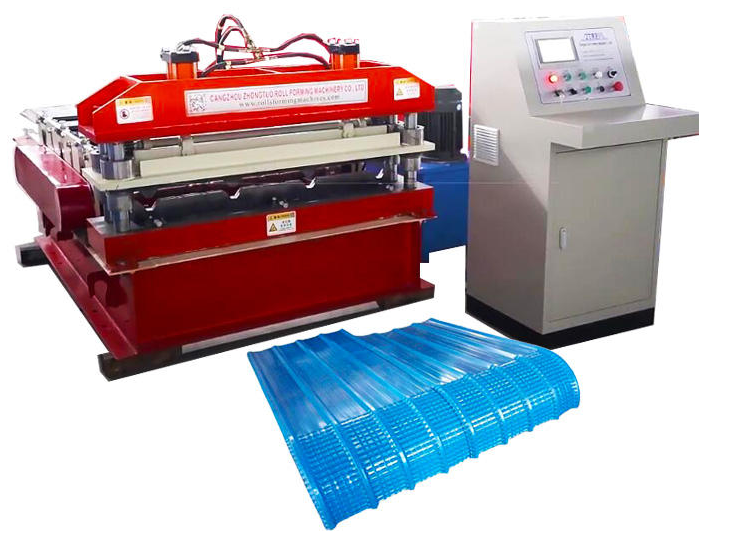
Design Concept:
This hydraulic arch cambering machine is designed to create precise, subtle curves in roofing panels for specific applications. By forming these curved panels, it significantly reduces the need for roof purlins and steel supports, offering a cost-effective solution for roofing materials. Additionally, the arched roofs produced are not only robust and long-lasting but also aesthetically pleasing and modern in appearance.
A curved metal roof is a structural design that merges innovation with functionality, and it is increasingly utilized in industrial, commercial, and public buildings. This article will examine the fundamental concepts, types, production methods, and material recommendations for curved metal roofs.
What is a Curved Metal Roof?
A curved metal roof refers to a roofing system where metal panels are laid along a pre-designed curve, creating a smooth, streamlined aesthetic. This type of roof not only fulfills aesthetic requirements but also boasts superior performance, such as excellent water resistance, durability, and structural integrity.
Types of Curved Roofs
The variety of curved metal roof designs offers architects, designers, and building owners numerous options to meet different architectural needs and stylistic preferences. Whether it’s the precision of factory-produced panels, the artisanal charm of hand-bent shapes, or the dynamic texture of corrugated sheets, each type offers a unique aesthetic that can enhance the overall design of the building.
Directions of Metal Panel Bending:
- Longitudinal Bending (along the length of the panel): This method is used primarily for large-span arch structures where continuous curvature is desired.
- Transverse Bending (along the width of the panel): Often used for short-span curved roofs, this bending method is easier to install and requires less complex machinery.
- Bidirectional Bending (combining both longitudinal and transverse bends): This technique is applied to create more complex geometric shapes, enabling highly customized roof designs.
Benefits and Drawbacks
Advantages:
– Aesthetic Appeal: Curved roofs provide a modern, visually striking appearance that enhances the building’s overall design.
– Improved Drainage: The curved shape naturally facilitates the flow of water, reducing the risk of water accumulation and leakage.
– Structural Stability: The arch-like structure distributes weight evenly, offering greater resistance to wind and seismic forces.
Disadvantages:
– Complex Manufacturing: Curved roofs require specialized equipment and technical expertise for fabrication.
– Higher Costs: Due to the complexity of the design and manufacturing process, curved roofs are typically more expensive than flat roofs.
– Maintenance Challenges: Repairing curved roofs may require specialized tools and techniques, making maintenance more difficult and costly.
Manufacturing Curved Metal Roof Panels
To produce curved metal roof panels, a curved metal roof roll forming machine is used. These machines are specifically designed for the production of curved roofing panels, which are commonly found in large-scale architectural projects such as sports arenas, exhibition halls, and transportation hubs.
Key Features of a Curved Metal Roof Roll Forming Machine:
– Material Compatibility: The machine can process a wide range of metals, including galvanized steel, aluminum, and copper, typically in thicknesses from 0.3mm to 1.2mm.
– Curving Capabilities: It can produce both convex and concave curves, enabling the creation of diverse and intricate roof designs.
– Automation: These machines are equipped with programmable logic controllers (PLC) for precise control, ensuring consistent product quality and efficient operation.
– Adjustability: With adjustable rollers and dies, these machines can accommodate varying panel widths and curving radii, offering flexibility for different design requirements.
Technical parameters of Curving machine:
Hydraulic Curving Machine Metal Roof Panel Bend Machine | |
Thickness | 0.18-0.8mm (0.18-0.3 hard material HRB65) (0.3-0.7 soft material) |
Motor Power | 3 KW |
Curved Radius | Min 2000mm |
Speed | 8-10m/min |
Voltage | 70 mm |
Shaft material | 45# steel with tempered |
Raw material | PPGI GI |
Roller material | 45#steel Chrome Plated |
Machine basic frame | 350# H steel welded with diagonal bracing inside |
feeding rollers | 3 stations, Cr12 steel with quenched treatment 60-62℃ To feed the steel sheet to pressing system |
More pictures of machine:
Technological process Coil car—–uncoiling—straightening —-shearing machine—–stacking and piling system Brief introduction of the line ZT-12X1500 cut […]
Mar. 13th 2025 Cangzhou Zhongtuo’s Aluminum Drip Edge Flashing Roll Former Revolutionizes Production for American […]
Key Features Of Trapezoidal Standing Seam Roofing Machine Include: 1.0″ Mechanical Seam Panel seam: 1” […]
1.5″ Form Deck Roll Forming Machine Profile: Standard Cover Width: 36″ Additional Cover Widths Available: […]
STAY IN THE LOOP