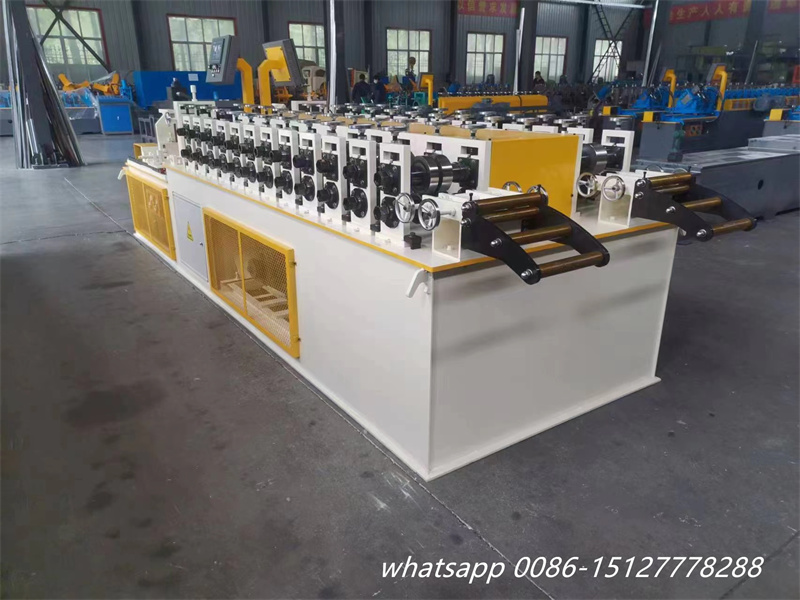
Description of the L-Track Roll Forming Machine
The value of an L-track tool is often underestimated until its practical benefits become apparent. Once you experience its functionality, you’ll quickly discover numerous ways to use L-track, especially as a flatbed driver. This light-gauge galvanized steel utility angle is highly versatile and serves in various applications, including column framing and bulkhead construction. ZTRFM offer an extensive selection of L-track systems, complete with hooks, tacks, fittings, and other essential accessories, recognizing the importance of these tools in a wide range of industries.
The universal light-duty L-track fitting is designed to be compatible with all types of aluminum load track systems. With these fittings, you can easily attach nearly any item to the aluminum track and, if needed, reposition components along the track by simply drilling new holes in the desired locations.
For light-duty loads that don’t require traditional winches or tie-downs, L-track is the ideal solution. It’s easy to install, user-friendly, and incredibly efficient. If you’re seeking L-track solutions, we are likely to have exactly what you need, as all of our L-track stud fittings meet the same high standards as our other products.
How the L-Track Roll Forming Machine Works
Like most roll forming machines, the process begins by feeding sheet metal into the system from the decoiler positioned at the rear. Once the material enters, it passes through the roll forming mill, where a series of fixed rollers gradually shape it into either an L or J profile. After the profile is formed, a hydraulic post cutter trims the material to the desired length, after which it is transferred to a hydraulic station and exit rack, making the finished panel ready for use.
The entire process is controlled by an advanced system that ensures both reliability and cutting-edge performance. The use of a roll forming machine offers several key benefits:
– High strength and durability
– Large working load capacity
– Consistent product quality and output
– No deformation during cutting
– Excellent uniformity in the final product
This machine can be customized to meet the specific needs of each client, making it a versatile solution for a wide range of applications.
Why Should You Invest in an L-Track Roll Forming Machine?
As labor costs continue to rise and machinery technology advances, automated, high-quality equipment for routine tasks has become increasingly appealing. If you are uncertain about the value of this investment, we assure you that our machines provide an impressive return. They are designed to accomplish tasks that would otherwise require hours of manual labor in mere minutes, significantly boosting your overall profitability.
L and J trim machines are continually evolving, becoming more cost-effective with each iteration. For any forward-thinking business owner, failing to invest in such technology is a missed opportunity. Since 2009, we’ve been a trusted name in the industry, with thousands of satisfied customers. Our machines are built with precision and come with a one-year warranty covering both parts and labor. So, why wait? Contact us today to secure yours!
Key Features of the L-Track Roll Forming Machine
Here’s a brief overview of the process involved in the operation of an L-flashing roll forming machine:
1. **Material Feeding**: The process begins with a coil or sheet of metal, typically steel or aluminum, which is fed into the machine.
2. **Roll Forming**: The metal then travels through a series of rollers that progressively shape it into the required L profile. These rollers are designed to create the precise dimensions and angles needed for the L flashing.
3. **Cutting**: Once the metal reaches the correct shape, a cutting mechanism trims it to the specified length. Depending on the machine’s configuration, various cutting methods—such as shearing, flying cutoff, or rotary cutoff—can be employed.
4. **Stacking or Coiling**: After cutting, the finished L flashings are either stacked or coiled for further processing or packaging.
L-flashing roll forming machines are generally customizable, allowing the production of flashings in various sizes, materials, and profiles to meet the specific needs of construction projects. They ensure high precision, efficiency, and consistency, making them essential for metal flashing production within the construction sector. The selection of materials, thicknesses, and additional features can be tailored to suit individual project demands or manufacturer preferences.
Profile Drawing :
The L Trim And J Trim Roll Forming Machine Working Flow:
The Technical Specifications Of The L Trim And J Trim Roll Forming Machine:
J Trim profile rolling forming machine |
||
1.Material of coil | Material Thickness | 0.3-0.8mm galvanized sheet full hard 85-95, G550, PPGI |
2.Forming system | Rolling Speed | 0-10 m/min( without the cutting time) |
3.Main body
|
Roller Stations | About 16-18 stations |
Roller Material | 45# Steel with quenching 60mm shaft | |
Maim Motor Power | 5.5 kw | |
Hydraulic cutting Power | 4 kw | |
Bearing | Rubber sealing bearing | |
Material Of Cutting | CR12 with quench treatment | |
Hardness | HRB 85-95 | |
Tolerance | +-1.5mm | |
4.Cutter | Cutting way | Stop cutting |
5.Voltage | Electric Source | 380V 50Hz 3Phase
Also can satisfy Customer’s require |
6.Control system | Control System | PLC Delta |
Inverter | Delta | |
Weight | About 2.5 tons | |
Way Of Drive | 1 inch single chain | |
Size of machine | Length 7500mm* Width 800mm* Height 500m | |
MOTOR | Under the frame of the machine |
More Pictures Of The Machine:
Light Gauge Steel Framing Machine Specification Width(web): 89mm Height(flange): 41mm Lip:7-12mm The machine match with 3 sets […]
Technological process Coil car—–uncoiling—straightening —-shearing machine—–stacking and piling system Brief introduction of the line ZT-12X1500 cut […]
Mar. 13th 2025 Cangzhou Zhongtuo’s Aluminum Drip Edge Flashing Roll Former Revolutionizes Production for American […]
Key Features Of Trapezoidal Standing Seam Roofing Machine Include: 1.0″ Mechanical Seam Panel seam: 1” […]
STAY IN THE LOOP